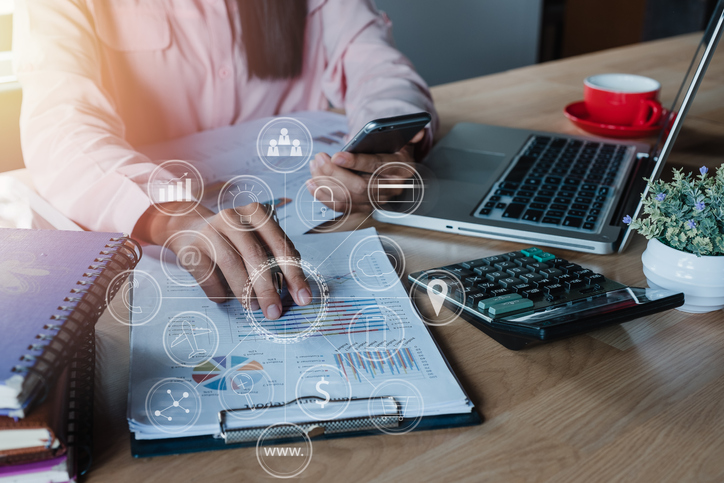
In an ecosystem, everything is connected. Supply chains are complex ecosystems, so quickly assessing the short and long-term impacts of events is a formidable challenge. We all know that the faster these assessments can be made, the better chance we have of making decisions that will mitigate risk and supply disruptions. For instance, the case study about P&G rapidly adjusting its plans to respond to hurricanes is a classic example of making fast assessments amidst disruption.
While we intuitively understand the value of rapid decision-making, it’s been difficult to quantify and provide an ROI analysis supporting investments in digitalization of supply chains and concurrent planning. This is because disruptions typically impact a limited number of sectors and enterprises with several variables including duration of disruption, geographic variations and any related impacts from simultaneous events. These factors make it challenging to create accurate assessments before, during and after a disruption.
And then along came COVID-19. The pandemic’s impact was global, across all sectors and almost all enterprises, with a duration of well over a year, with a clear start and relatively clear ending (except for China).
Morgan Swink, Professor of Supply Chain Management at Texas Christian University’s Neeley Business School and Executive Director of the Center for Supply Chain Innovation at Texas Christian University, saw this as the perfect opportunity to test the theory that faster assessments and decision-making drive superior financial outcomes. Professor Swink conducted research across 644 firms across six industries with an average quarterly revenue of $4 billion and total assets of $35 billion. Of these companies, 48 use Kinaxis RapidResponse, an advanced system for supply chain planning. His research spanned three years starting with Q3 2019 and analyzed publicly available financial data.
Professor Swink’s data showed that, on average, companies who’d deployed RapidResponse had a cumulative 7.7% superior Return on Assets (ROA) over three years versus companies who had not. For a company with $10B in total assets, this would result in a $770M benefit over three years.
Next, Swink compared financial data during the pandemic to demonstrate the drivers of these ROA results:
- Kinaxis companies reported improved revenue during the pandemic while their peers lost revenue.
- All companies increased inventory but Kinaxis customers did so to a much lesser extent.
- Kinaxis customers saw a decrease in cost of goods sold (COGS) while their peers saw an increase.
Professor Swink’s conclusion is that CFOs and the financial community at large need to understand supply chain planning’s impact on financial outcomes and aggressively invest in advanced capabilities and solutions. In fact, this should be considered part of an enterprise’s digital transformation and go hand-in-hand with Industry 4.0.
Concurrent planning is key for enabling faster reactions to challenges, creating a supply chain that’s completely connected and always in sync. Through the creation of a digital twin and a solution that provides visibility, transparency of impacts, and rapid scenario analysis, a company can drastically shorten the cycle between planning and execution and create a competitive barrier.
Watch our on-demand webinar to dive into this topic further with Professor Swink, who's joined by Blaine Fitzgerald, Kinaxis Chief Financial Officer and Anne Robinson, Chief Strategy Officer at Kinaxis.
Additional Resources
- Supply chain management frequently asked questions
- Supply chain transformation frequently asked questions
- Concurrent planning frequently asked questions