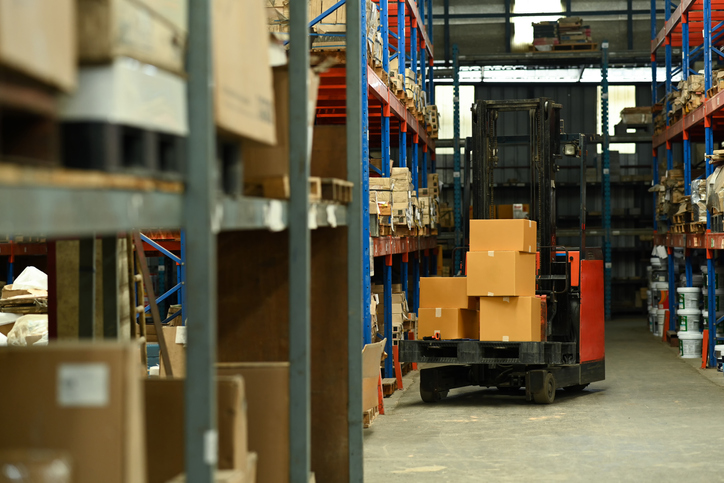
We are living in a world that is vulnerable to changes, especially in supply chains. Planners are making an extensive effort to improve demand plans and supply plans throughout their supply chains. However, aligning demand and supply isn’t as easy as people think nowadays, given that fluctuating demands, over- or under-supply issues, and transportation delays may all lead to unwanted chaos in other areas of the supply chain. Inventory management, for example, has been a challenging task for planners who are struggling with a disconnect between demand and supply.
According to recent statistical data, vacancy rates for industrial real estate across North America have been declining since 2020 and reached an all-time low in the third quarter of 2022. As a result, inventory managers have to explore new ways to cope with full warehouses. The COVID-19 pandemic is undoubtedly to blame for the warehouse shortage. During the pandemic, consumers turned more frequently to online shopping and triggered multiple shifts in buying patterns that resulted in the soaring demand for products. Consequently, while others are celebrating a relative end to the pandemic, retailers are facing unwanted inventories piled up in warehouses.
It’s not only natural disasters, production delays, or travel restrictions that can disrupt supply chain plans, but also availability of workers, who play a bigger role nowadays. One of the recent examples is the freight strike in the UK in late August 2022 that led to a 24-hour stoppage and congestion in distribution networks. Even with well-planned inventory management on a routine basis, planners may not have been able to predict the strike, or the direct result of even more excess inventory filling up warehouses.
Unconventional solutions to excess inventory challenges
Big retailers are coping with the excess inventories by acquiring extra space to place their stockpiles of goods. In response to this quick action, real estate costs have risen due to companies’ higher willingness to pay. Paying a higher price does solve the problem temporarily for large retailers, however, high leasing rates and scarce storage space are squeezing small businesses out of the warehouse market. Unused stockpiles of goods have forced these companies to find alternative spaces that will not be obtained by big competitors.
As a result, unconventional storage spaces, including shipping containers and truck trailers, are being used as temporary warehouses by small retailers. This new overflow strategy has mitigated inventory imbalance due to the scalability and mobility of transport equipment. Although such an ad hoc arrangement appears to have resolved the storage shortage, it does not mean retailers can keep the whole supply chain running without any more disruptions. Occupying transport equipment for inventory storage will inevitably add stress to existing supply planning as containers and trailers are tied up for inventory placement. The resulting adverse effect on supply plans further disrupts the original transportation of goods, worsening the shrinking capacity of storage space to hold any increasing inventories.
Planners might be pondering: What can we do to avoid such a catastrophic mess in supply chains? How can we plan so that businesses won’t get caught up in unexpected situations that jeopardize the running of the whole supply chain? The answer goes beyond standard inventory management. Inventory management is not a siloed task that is separated from other functions in supply planning. Rather, it needs to be concurrently embedded in all planning activities to help break silos and connect all parts of supply chains. In a perfect world, inventory managers will be notified by advanced planning tools when a change occurs and has an impact across the whole supply chain, including inventories. The end-to-end visibility allows them to respond to real-time scenarios and make plans accordingly. For instance, the aforementioned emerging buying pattern and week-long freight strikes can be sensed when planning, and therefore, concurrent planning technologies provide adaptive solutions in inventory management to accommodate up-to-date demands and supplies. Moreover, inventory management not only requires well-performing planning but also calls for efficient execution to ensure the completion of plans. Shortly, inventory managers are expected to benefit from execution applications including warehouse management systems and transportation management systems that are empowered by advanced planning tools.
Kinaxis strives to fulfill the vision of future inventory management. With Kinaxis RapidResponse®, inventory levels across the entire distribution network are optimized with complete end-to-end visibility, enabling planners to identify and resolve issues faster and more accurately.