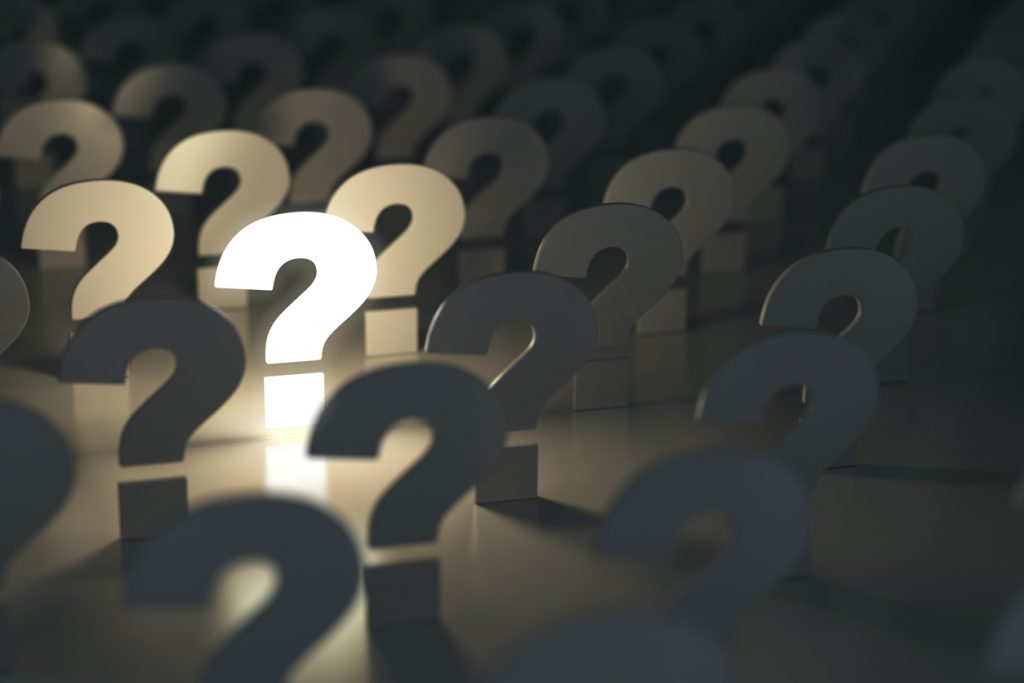
CSX, one of the only two railroad operators in the USA that handles nearly all the shipments that move by train east of the Mississippi River has been experiencing serious challenges since the month of May. The reasons behind this were well chronicled in a recent Wall Street Journal article.
To sum it up, an activist investor caused a major shakeup in the company earlier this year and a new CEO took over in March. The new CEO embarked on several cost reduction initiatives in conjunction with a number of changes (some may argue too fast and too soon) on how the company operates its freight-trains. This has resulted in significant delays and disruptions in shipment deliveries.
An extreme example of this is a ride from Chicago to Colesburg, Tennessee taking 18 days, 13 hours, and 57 minutes! The effects of these delays are being felt by many companies including McDonalds, Kellogg, Kraft-Heinz, and PepsiCo, as the article cites. These companies had to haul expedited shipments by truck so they could keep their production lines running and, in turn, meet the commitments to their customers. This has led to increased costs, not to mention all the inventory stuck in-transit.
Needless to say, such major challenges are visible enough and have significant enough disruptive power that considerable energy gets spent on addressing them, including executive engagement. However, did you know there are enough lead time problems lurking in your current supply chain operations that go completely unnoticed? These are the “knowable unknowns” that can hurt your supply chain performance.
Over the years, I have partnered with a number of customers across a variety of industries as part of their supply chain planning transformation journey. While implementing a technology solution, a lot of time is spent on cleaning the master data including assumptions around capacities, lead times between nodes, yields and such. However, once the implementation is live, many of these assumptions tend to stay static and are seldom touched.
Over time, such assumptions have the potential to drift away from the reality, causing significant downstream execution challenges. For example, let’s say you modeled the lead time from “supplier A” to your manufacturing facility as 7 days. If the supplier performance degrades gradually and on average the supplier is now taking 10 days to deliver, you get into a constant firefighting mode with inventories running low, regardless of how good your planning algorithms are. On the contrary, if the supplier has significantly improved the performance and is able to consistently deliver in 5 days, you may miss out on the opportunity to be leaner. Such gradual degradation of planning assumptions can be performance killers to your supply chain, causing the users to lose faith in the planning system and resort to the all too familiar Excel.
Often times, someone in the procurement organization is aware of change in lead times through supplier monitoring/scorecarding, supply chain risk management and such. However, this information in most cases does not make its way back into the planning systems. I used lead time as an example here. But it could be any supply chain assumptions that go into your planning system, such as capacities, yields, order multiples, etc.
Today’s supply chains are far more dynamic, and underlying assumptions and data evolve rather quickly. Applying rigor and discipline to keep supply chain assumptions and the associated master data in sync with the reality is a must have to avoid “garbage in garbage out”. Those with experience in supply chain data quality improvements will attest to the fact that these endeavors are quite labor intensive. But these are exactly the kind of problems that can favorably be addressed by Machine Learning.
By mining through plan assumptions and leveraging the actuals from execution systems, learning algorithms and intelligent agents can make recommendations on what data elements need to be corrected. In addition, these algorithms can also detect and surface the persistence and pervasiveness of such anomalies across the entire network, predicting risks and suggesting resolutions. These algorithms offer the potential to autotune the supply chain assumptions as they start deviating.
Poor supply chain assumptions are like the deep cuts and bad bruises on your supply chain. However, by leveraging these emerging technologies, we enter the world of supply chains that can heal themselves!