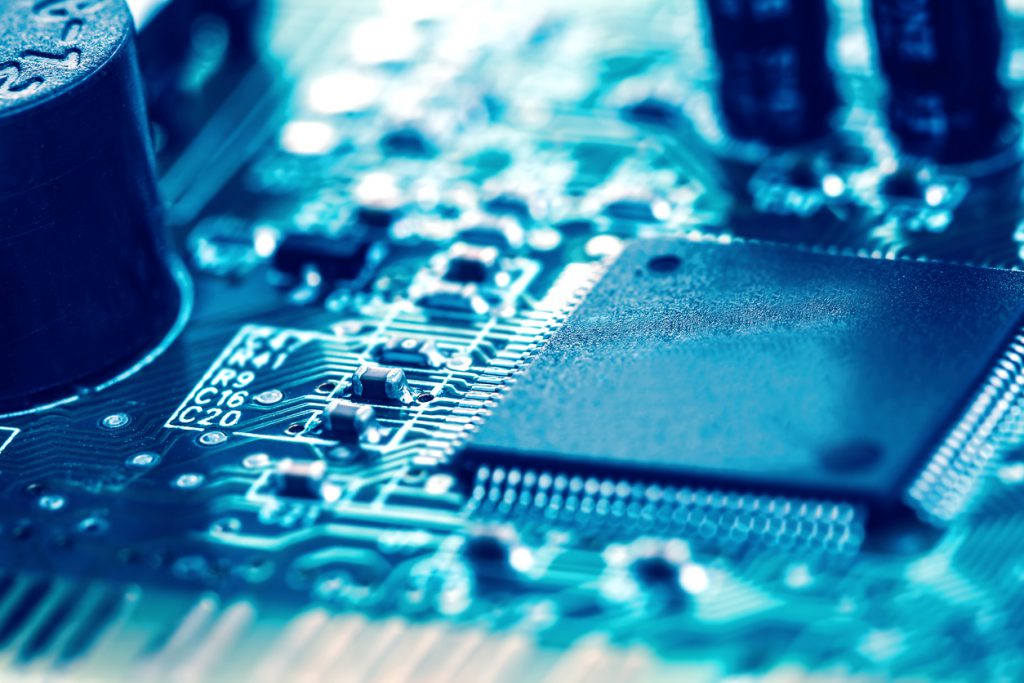
5 hurdles the semiconductor industry needs to jump over to find success
Building your business on someone else’s supply chain blueprint may not be the best way to find success. What works for one company may not work for another – especially if they’re in varying industries, geographies or are different sized enterprises. As I noted in my earlier blogs in this series on consumer electronics and life sciences, each industry has unique supply chain pain points that need to be overcome to improve efficiency and profitability. When it comes to the semiconductor industry, one of their biggest supply chain hurdles is that the speed of new technology introduction is 2-3X faster than the research and development (R&D) timeline. It’s a highly capitalized industry thanks to the high cost of fabrication centers (Fabs). It’s transforming from design and manufacturing companies into design and product companies. These new fab-less companies are working with foundries to manufacture wafers, instead of fabrication centers. The cyclical nature of the semiconductor space requires impact mitigation through product expansion (portfolio diversification) and rapidly scaling capacities. The result is an increase in mergers and acquisitions (M&As) to stay competitive, leading to disparate processes, systems and tools. Here are a few other challenges the semiconductor supply chain has to face.
Front-end (FE) manufacturing output requires added manufacturing steps
FE outputs like wafers or dies, require additional manufacturing steps like assembly and testing and a blended model. This drives complexity across the supply chain, making efficient capacity planning extra difficult. Solution: Allocate capacity across multiple sites, business segments and/or products to minimize the impact of site-specific constraints. You’ll also need to have the ability to compare multiple capacity allocation scenarios to determine the best option for back-end (BE) capacity allocation. This minimizes customer impact and maximizes profitability.
FE cycle times are much faster than BE cycle times
FE cycle times are typically 6 to 8 weeks, while BE cycle times are only 1 to 2 weeks. That means postponing inventory at various manufacturing stages, which requires additional planning. Solution: Inventory postponement planning and late-stage differentiation for BE are critical to managing working capital and to provide improved capacity flexibility. It’s best to use an analytics-based strategic policy for this to mitigate forecast error, factory excursions and the impact of natural disasters.
Limited end-to-end supply chain visibility and planning
Multiple direct and indirect materials required for manufacturing, and unconnected internal and contractual manufacturing sites and distributions centers, makes supply chain visibility difficult, learning to excess inventory growth and poor customer service. Solution: Integrate all disparate systems for easier planning and greater visibility. This will drive greater comprehension of multi-tiered sourcing and manufacturing constraints, enabling integrated planning, scenario analysis and better, faster decision-making.
Customer-specific requirements
The same product often has different material, site, quality, manufacturing, shipment size, etc. requirements, all based on each customer’s individual demands. There’s also rarely a formal forecast applied to samples requested by the customer, or the cost and capacity requirements associated with them. Solution: Using attribute-based capacity planning, tracking customer attributes for multiple customers in multiple product tiers is easier. Without it, human glue is the only thing holding things together – making the process error-prone and highly inefficient. And don’t forget to add samples to your planning for early stage SKUs and product families. This will provide a clearer picture of capacity and the cost of doing business.
Data latency
Power, performance and function-based binning of wafer-die can result in multiple co-products from the same wafer. Different functions, each using different planning parameters, causes data latency issues because that data is housed in multiple, disparate systems. Solution: You should monitor and update planning parameters in a single system through scheduling, which will enable you to see the most recent official parameters available and work from one single source of data truth. Early visibility into project planning parameters gives insight into potential co-products to drive early demand shaping actions. That way you can ensure co-products are consumed and profitability is increased. These are just a few of the specific semiconductor supply chain pain points. What other challenges are you facing in your supply chain? Let us know in the comments section below. And don’t forget to check out the other industries featured in this blog series:
Stay tuned for the next instalment when we take an in-depth look at the supply chain challenges the automotive industry faces.