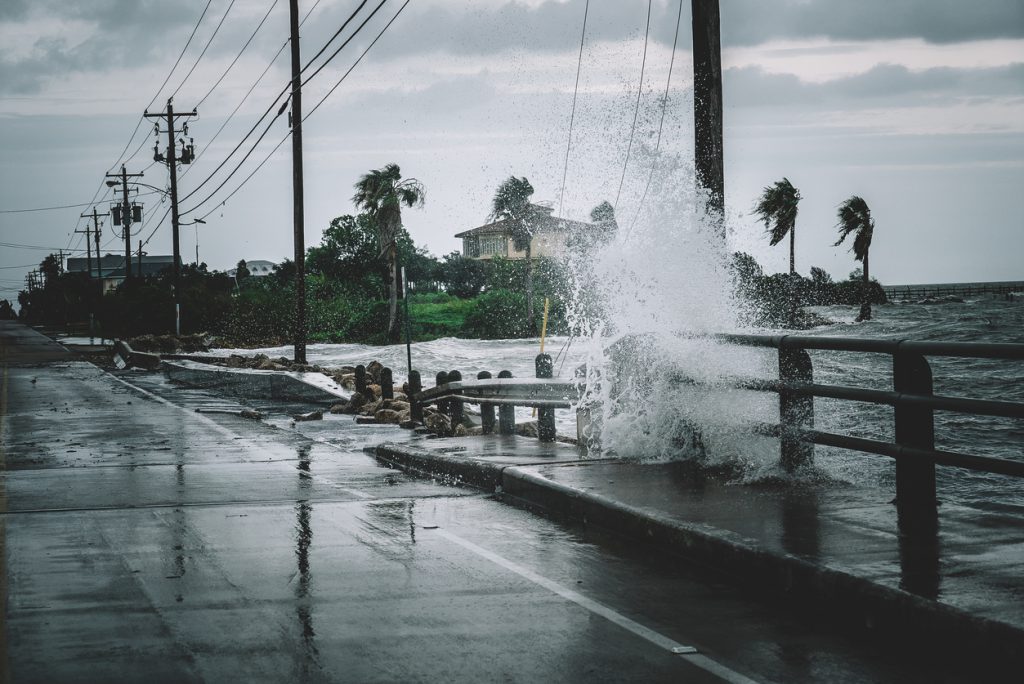
If you had anything to do with supply chain planning in the early days of enterprise resource planning (ERP), you may consider those years the “good ol’ days”. Spreadsheets were the latest and greatest thing, your biggest headache was a supplier failure, and collaboration meant walking down the hall to visit with your buyer or dropping by the shop floor to check on a machine breakdown.
Times have changed. Supply chain planners (I’m lumping in all the silos, including demand, supply, inventory and capacity planning) today are dealing with challenges that were unimaginable when Lotus notes were the next big thing.
Arguably, changes to the good ol’ days started with product proliferation, increasingly shorter product life cycles, globalization and a more educated, demanding customer. Aligning the supply plans to these new volatile demand profiles was no easy achievement.
However, none of this physically destroyed your supply chain. The increase in extreme weather events is becoming commonplace for the supply chain community and the challenge of managing around these supply chain disruptions is the new norm.
Natural disasters and supply chain disruption
It would be easy to talk climate change and the causes behind them but that would be irrelevant to this discussion. Let’s just look at some events:
- 2017 – Hurricane Irma (plus others)
- 2016 – Hurricane Matthew (plus others)
- 2015 – Nepal earthquake, 7.8 magnitude
- 2014 – California wildfires (150 homes destroyed, massive power outages. The year seems to be interchangeable, just looking to get wildfires on the list.)
- 2013 – Massive tornado packing 200 mph winds in the Oklahoma City area. (See 2014 side note)
- 2012 – Hurricane Sandy
- 2011 – Japan earthquake / tsunami and Fukushima disaster
- 2010 – Haiti earthquake
I’ll stop there. It wasn’t hard to find numerous examples for any given year in the past decade. Even if for some unknown reason you think climate change is a hoax, it doesn’t matter, these events will continue to be the new way of life for all of us, including supply chain practitioners. According to the New England Journal of Medicine, there were three times as many natural disasters between 2000 and 2009 compared to 1980 to 1989.
Planning for natural disasters in the supply chain
For any single event, supply chain planners now must deal with increased demands, limited supplies, risk to transport networks – which could include physical damage or people supporting the network not being able to get to work – and pricing spikes to fuel and other limited commodities. For a small bit of good news, supply chain leaders know this and are putting strategies in place to deal with this new reality. The technology is there to support the risk preparedness, including:
- End-to-end network visibility
- Global collaboration
- Quick scenario / resolution modelling before and after the event
See my blog on Hurricane Irma and the things planners are doing to prepare for catastrophic events. I may have exaggerated adding “storm chaser” to the supply chain planning title. I doubt any planner will be starring in the remake of the movie “Twister” anytime soon, but these people will be as tuned in to these new realities as much as any meteorologist. However, calling the supply chain planner a “network” planner is something worth considering.
Given how critical and time sensitive any response is to managing the aftermath of a natural disaster, can we afford for assessments and solutions having to go through a number of functional silos before they’re put into action? Is there a way to speed up the preparation and response times for these extraordinary situations?
Although improvements are being made to supply chain planning as part of the recognition that severe weather events are a regular challenge to deal with, it’s being done on the foundation that supports the normal mode of operation. Perhaps we haven’t reached the tipping point for the network planner. The technology is surfacing that would support a new mode of operation, but are the functional experts still too engrained in our supply chain processes?
I know a number of demand planners and forecasters who, as statistical gurus, could hold their own with any seasoned mathematician. Is running a multi-echelon inventory optimization even something a capacity planner has interest in? They may be too busy looking at constraint challenges or alternate sources of supply. Much like artificial intelligence (AI) and machine learning (ML), there is still a lot of hype about the network planner. But like AI and ML, network planning is grabbing the attention of supply chain leaders. It’s just a question of priority.
Will it be something that we evolve to as part of supply chain transformations, or will it be out of necessity and a need to manage the new supply chain planning landscape? Your guess is as good, if not better, than mine. I haven’t met a network planner yet, but I’m looking forward to that day. Let me know how soon you think network planners will be handing out business cards.
Additional Resources
- Inventory optimization frequently asked questions
Leave a Reply