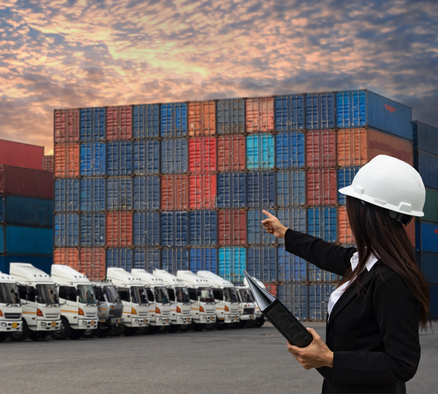
Exclusive Partner blog post
In the fast-paced VUCA (volatility, uncertainty, complexity and ambiguity) environment that emerged after the pandemic, supply chain management and operations have become more critical than ever before to a business’s competitiveness. Businesses’ top concerns include meeting customer demands, optimizing capacity to navigate volatility, meeting sustainability goals and finding skilled labor. How can businesses ensure they remain competitive in such a market while facing constant pressure to improve efficiency, reduce lead times and cut costs?
Businesses with highly successful supply chains depend on practices like end-to-end coordination, process harmonization, clarity of decision rights and a cross-functional performance system. Eliminating planning silos and building streamlined processes with a proper IT infrastructure are critical for a company’s success.
Siloed planning blocks visibility and creates inefficiencies in material and transportation planning
Often, the functions of material planning and transportation planning and execution are performed in silos. These two processes are critical in supply chain, and yet neither one has visibility over their impact on the other:
- A material planner has no transparency over their impact on transportation execution. The products and material deliveries are planned without taking real-world transportation constraints into account, such as truck capacities, schedules or incompatibilities. This can translate into a non-actionable plan and require significant last-minute changes before transportation execution.
- A transportation planner has no transparency on the impact of transportation on inventory level. Transportation is executed without considering material availability, inventory level or storage capacity. This can create further delays and necessitate additional transportation arrangements, for instance, if the material is not ready at the plant.
This gap creates several inefficiencies, like higher transportation costs due to last-minute plan changes, low truck utilization and overall planning inefficiency.
So, the question becomes: how can we bridge this gap? 4flow and Kinaxis answer this question by bringing transportation optimization and load building capabilities directly into the S&OP processes.
What is load building?
Load building is the process of combining multiple orders into a single shipment to maximize vehicle utilization and reduce transportation costs. It can be done with a transportation planning system and has a significant impact on a company's profitability.
Conventionally, transportation planning and load building are part of transportation execution processes. But what if you could optimize and plan loads earlier in the supply chain processes – before the scheduling agreements are set, and when the demand and supply plan is more flexible and can be adapted to real-world constraints?
The flexibility gained from earlier load optimization unlocks important benefits. Planners avoid expensive last-minute changes in the execution. Back-and-forth communication to adapt the transportation plan between suppliers and carriers is minimized.
The Transportation Load Optimizer, an embedded RapidResponse application, empowers planners to automatically and simultaneously consider transportation and S&OP constraints, ensuring optimal planning: the results are feasible and cost-efficient, and material arrives on time.
What is the difference between a transportation planning system and a transportation management system (TMS)?
Integrating transportation planning and optimization earlier in supply chain processes does not replace a TMS. But early transportation planning can enhance the execution and use of a TMS system for even greater supply chain resilience.
A transportation planning system and a TMS have different uses and operate with different planning horizons. A transportation planning system is a planning tool with an optimization horizon that ranges from 3 days to 3 months, depending on your requirements. A TMS is an execution tool which typically operates in a very short window of time, the next 24 to 48 hours.
The benefits of these two systems differ, as well. A TMS enhances day-to-day visibility, provides compliance and documentation, and supports timely delivery of goods. On the other hand, a transportation planning tool focuses on load building and optimization capabilities and aims to maximize utilization, reduce transportation costs and improve planning efficiency.
Another critical difference is optimization capability. A TMS can only optimize your known transportation factors. A TMS receives the orders from the MRP run just a few days before the actual delivery. There is no visibility on the impact of the inventory level. For instance, the material availability is not visible to the planners, so it is not possible to know if there are any conflicts with the execution itself.
A transportation planning system can add an automatic step to S&OP processes and optimize your demand and supply data considering transportation constraints. It allows you to consider and optimize transportation factors and S&OP constraints simultaneously.
How can transportation planning enhance a TMS?
The main advantage of integrating transportation planning software is that demand and supply planning can be optimized considering transportation from the start. This makes execution run more smoothly, as planners do not need to adjust the orders’ deliveries to fit operational constraints.
This full visibility also gives material planners an understanding of the impact on transportation execution, ensuring an actionable plan. At the same time, transportation planners are aware of inventory levels and material availability. This streamlined process eliminates silos and allows businesses to have full transparency and greater planning efficiency.
Greater flexibility comes from earlier planning and optimization. In addition, businesses can share planning information with the carrier base prior to the load tendering. This can help overcome the capacity constraints we’re currently seeing in the transportation market and even help drive rates down because you're providing an advanced preview.
Adding transportation and load building optimization in the early stage of material planning is a key lever to eliminate silos and ensure both efficient and reliable planning. Armed with an actionable plan, businesses gain resilience and maintain peak performance: a strong strategy to overcome supply chain complexity and stay competitive in today’s challenging market.
If you’re interested in discovering more about the Transportation Load Optimizer, the RapidResponse application for load building and transportation optimization, contact us.