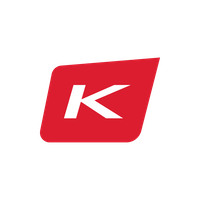
Most manufacturing enterprises have a formal approach to planning and executing production. However, it seems that at a practical level, there is some combination of planning and executing as well as expediting (working to recover to meet late or potentially late demand). I think that most of us would agree that ideally, we would have a sound plan where there is accurate demand (forecast and/or actual), adequate resources and capacities are in place both in-house and at suppliers, and all the supply chain is on board and executing to the plan.
In reality, there is a lot of expediting that occurs, at least in my experience (the extent of which depends on the industry and the complexity of the products and the supply chain). A lot of manufacturing companies even have a formal position with a job title something like “Material Expediter” or “Production Expediter” (although the actual job descriptions can differ from what I am describing). What I have found in working with some customers who do a lot of expediting, is a basic lack of maintaining data accurately in their formal ERP/MRP system.
A lot of the “planning” tends to occur off-line in Excel spreadsheets or other tools. This may work in some isolated areas, but from an overall enterprise perspective, much of the supply chain does not have visibility into these off-line plans. I correlate this to Project Management on a large project where there is no up to date project schedule that the entire project team can work to.
Team members work tasks that they are directed based on meetings, phone calls and other types of somewhat ad-hoc communication. This can be somewhat effective, but not having the formal MRP system reflecting the current plan disables the capability to orchestrate the entire supply chain and efficiently execute the plan. This leads to a lot of expediting rather than planning and executing. Why don’t we always keep the formal MRP system up to date? There are lots of reasons, including:
- too time consuming;
- off-line tools are easier and more flexible; and
- certain processes or functionality is not supported in the formal system.
An example of # 3 above, is provided in a blog post from a colleague of mine called Do YOU have enough Supply? This describes a process to allocate limited supply to demands that recently, seems to becoming more prevalent in certain industries. A process like this may not be supported in the formal MRP system, so it is likely done off-line. Changing or enhancing the MRP system to support new functionality generally takes some significant time and money, and usually has to compete for priority with other fixes and enhancements needed. I know that many of you will agree that this expediting approach is far from ideal, and also may say "not us, not me". But I also know from experience that this occurs and sometimes with some very practical reasons. In situations like this, what can help solve the problem is a system with capabilities in a couple of key areas:
- Detect and report data integrity issues in the MRP system for clean-up
- Easily configurable to support additional planning functionality
- Available for sharing and collaboration across the supply chain
I would like to hear any insights, experiences and suggestions you may have regarding this expediting versus planning situation.