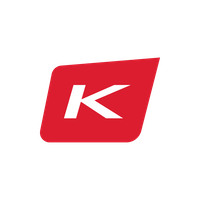
I’ve been thinking about this post for some time. I’m a Toyota customer. Our family has owned four Toyota Corolla’s over the past twenty years and we’ve always been very happy with them. Our most recent purchase, a 2010 Corolla S, has been a great car for my daily 160 Km (100 mile) commute. With a fuel mileage of 5.6 litres per 100 km (35 mpg) on the highway, I’m not cursing the oil companies with the vehemence I once did. On the other hand, this is the first time I can recall in all the years that we’ve owned Toyotas that I’ve had to deal with a recall. And so far, I’ve had two (brakes, accelerator pedal)...with a possible third (power steering?) rumoured to be in the works.
The Toyota quality problems have disappointed me. I learned about the Toyota production system when I was studying Industrial Engineering in college. At that time, it was held up as the future in manufacturing - a model that other manufacturers around the world should follow. It still is. At Toyota, defects are considered to be MUDA (waste) when they occur, the root cause is found and eliminated.
This is the cornerstone of their system. Since then, my studies in lean manufacturing have taken me deeper into the Toyota manufacturing system and my faith in the quality of their products has only improved. I expect better from Toyota...and I suspect Toyota feels the same way. Toyota has made mistakes: first the error that caused the problem in the first place, then the shoddy handling of the first incidents (which could be the result of disbelief that the problem could be caused by a manufacturing defect). They seem pretty confident now that they have the problem figured out. Let’s hope so.
What got me thinking is this... Here is this vaunted company, renowned for the fine quality of its products, with systems specifically designed to prevent quality problems from happening and especially from getting out of the factory. Yet, this company is running into some serious quality problems. Think about Toyota and their processes. Think about your company and your processes. Which company do you think would be less likely to run into this type of problem? What processes do you have in place to ensure that this doesn’t happen?
Here’s something more interesting. On February 1st, Toyota announced that they had figured out the gas pedal problem. On February 11th, I had my car in for an oil change and they told me they had the kit to fix the accelerator pedal so they would do that while my car was in. Toyota had the parts to address the sticking pedal recall days after announcing the fix. How long would it take your company to respond? I’m not trying defend Toyota. Like I said, they made mistakes – and it’s costing them.
What I’m trying to do is to have us learn from what Toyota has done wrong, and from what Toyota has done right. Who knows... The next time it might be your company facing a problem of this magnitude. Will you have the capabilities in place to respond? What do you think?