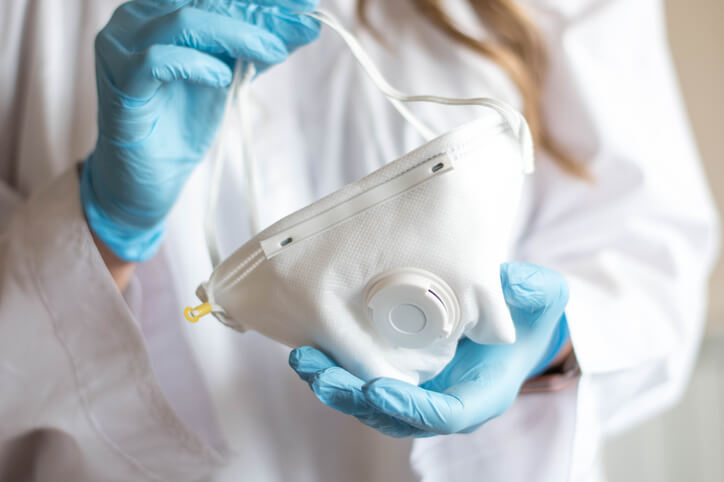
You can’t help but notice the significant run on products as people stockpile in the face of the COVID-19 pandemic. For those in supply chain, it makes you think that planning has gone down the toilet. Producers of toilet paper are a prime example of the supply chain challenges we’ll see.
A leading Canadian toilet paper manufacturer is working overtime to meet the demand. Dino Bianco, the chief executive officer of Kruger Products observed, "This thing continues to evolve, on so many fronts, but clearly I think it caught most of our industry off-guard." We are sure to see the full bullwhip effect of the situation. "We'll have a lull afterwards," he said. "Because at the end of the day, you're only going to use so much tissue."
There is no intent to make light of the current global situation. Unfortunately for the supply chain, it’s not as simple as a single demand spike. U.S. Senator Josh Hawley warned, "The coronavirus outbreak in China has highlighted severe and longstanding weaknesses in our medical supply chain. This is more than unfortunate; it’s a danger to public health.”
There’s more than one problem facing supply chains. Here are three main areas to think about as we make our way through uncharted territory.
1. Demand is all over the map
People are stockpiling items in preparation for the unknown. Everyday items like rice, canned goods and wipes are flying off the shelfs. This represents a spike that looks like Mount Everest. The concern for consumers is that daily household items will no longer be available. It’s always good to prepare, but it does strain the supply chain.
Of course, there are the expected spikes in surgical masks, gowns and test kits. There’s a need to hurry therapeutics, vaccines as well as temporary testing and hospital facilities. All have supply chain implications.
On the other side of the equation there are the demand slides. With sporting and entertainment events canceled, travel limited and people self-isolating, the items seeing demand cliffs are extensive. With demand spikes and cliffs, current plans and forecasting methods are of little value.
2. Supply shortages are inevitable
The life sciences supply chain is the most stressed to deliver medications to patients all over the globe. There is so much dependent on China. But on February 18th, the FDA put a hold on inspections of China’s facilities amid the outbreak.
This was only a start to supply disruptions, and at that time, the FDA warned of supply shortages. The FDA can do some things to mitigate the shortages, like extend expiry dates and expedite the review of alternate therapies. It’s hard to know how much these options will help without understanding how big the problem is.
Major manufacturing operations for a number of industries were hit hard in China. As well, India is blocking 26 active pharmaceutical ingredients (API) and finished products from export, making shortages almost inevitable. At best, companies would be looking at longer lead times. And it’s not that easy to identify and switch to alternate suppliers. There would be a need to review any contractual liabilities, quality issues or regulation impacts.
The shortages will extend to space and staff as well as the examples covered above. We'll see shortages of many items that were once well stocked.
3. Recovery is an unknown
It’s anybody’s guess when things will get back to normal. The unknown is the biggest difference between the COVID-19 pandemic and other major supply chain disruptions.
For example, major weather events like hurricanes and tornados are devastating, but as catastrophic as they are, there is usually a glimmer of hope as the recovery process starts. The major impacts are supply disruptions, and many companies have gotten better at planning and responding to this kind of supply chain volatility. Staging inventories, quick simulations to test alternate supplies and strong collaborative capabilities to participate with suppliers and customers during recovery are a few strategies that are commonplace now.
The pandemic is a different beast. It’s not one problem and there is no end date. In a recent post Lora Cecere warned, “Recovery is going to be long and knotty. We are writing a new chapter in supply chain risk management. The largest issue is the complexity of the global supply chain.” There are new levels of demand, supply, inventory and capacity volatility with COVID-19. The complexity of the global supply chain only amplifies the challenge of responding to the threat. Supply chains must continue to deal with the normal complexities as well as issues like Brexit, tariffs and ongoing weather events. This is on top of the global pandemic that has no immediate end in sight.
Managing the triple threat
Response and risk management will be a hot topic around boardroom tables all over the world for the months and years ahead as companies take lessons learned to up their supply chain response processes.
As supply chains focus on a response, surprise is the new norm. It seems like things are changing daily, even hourly. It doesn’t mean forget to plan. We still need to think about the next month, quarter and years ahead. Lora offers up some valuable advice, “Model based on actual market demand. Traditional sales and marketing data is also obsolete. There is no substitute for local market data.” She also suggests building a dedicated action team and taking care of your people.
People will get us through the challenges in front of us over the next weeks and months but they still need tools to do their job. Technology isn’t the only answer but a prerequisite for a solution will be strong collaboration capabilities. Any supply chain participant – from CMOs (contract manufacturing organizations) delivering APIs, brand owners and even patients – needs a seamless way to communicate and collaborate on response options and recovery strategies.
Speed is key
Collaborating at the speed needed to respond to today’s pandemic is predicated on the assumption you have a single place to collect data, simultaneously execute multiple supply chain functions and collaborate across the globe. It may be time to put functional silos out to pasture. Traditional methods are too slow and lack the agility needed for this new chapter of risk and response management.
Planning, responding and risk management processes will need to ask and answer multiple questions as fast as it would take you to read this post. The more unknowns there are, the more questions there are for the supply chain. What if the FDA extends expiry dates? What impact will that have on satisfying demand or resolving an API shortage? What do optimistic and pessimistic views of recovery look like? What’s the impact on delivery, revenue and margin? What if a supplier is not back online until April or May?
You need to get answers that you have confidence in, often and fast, and share them for collaborative resolution.
“Pandemic ready” supply chains
Coming out of recovery there may be new requirements placed on the life sciences supply chain. We already talked about the need for speed. There will also be new visibility requirements. Similar to the Sarbanes-Oxley Act of 2002 where there were requirements for all U.S. companies on how they reported financials, we'll see the same thing for reporting on the supply chain.
The Medical Supply Chain Security Act Senator Hawley put forward is asking that the FDA get even more authority. Health officials will be looking for visibility to details of manufacturing capacities for essential drugs and medical devices to protect vital medical products. Manufacturers will need to report on “imminent or forecasted shortages of life-saving or life-sustaining medical devices to the FDA just as they currently do for pharmaceutical drugs.” This will require life sciences companies to bring together all supply chain data into a single source and turn that data into information that could some day stand up in a court of law or Congress.
It’s understandable that all you want to do is cover your face with your hands when you think about demand volatility, supply constraints and unknown recovery dates. But we know that’s not good for many reasons: it won’t help and health officials are telling us not to touch our faces. Hopefully the word “recovery” will generate a small spark of optimism. History has taught us the human race is capable of pulling out of the depths of despair. In the meantime, we can “pandemic ready” our supply chains so we become experts at response and risk management.
Our new brochure, “5 disruption response best practices: Risk management for today and the future,” has recommendations to get you started. If you have any lessons to share that would help others, we’d appreciate hearing about them. And one other ask: please stop hoarding the toilet paper.